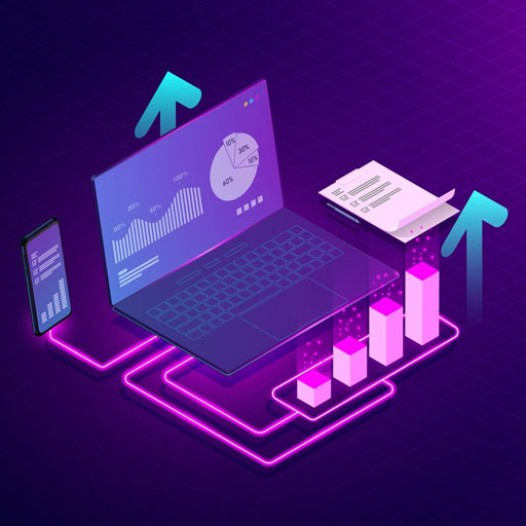
What We Do
Transform your business into a high-performance organization with our ERP solutions
Unlock your business's full potential with complete visibility and control. Leverage real-time data to make informed decisions and drive growth with Datamation ERP Solutions.
Our Business Stats
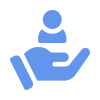
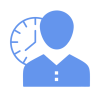
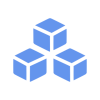
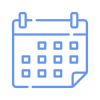
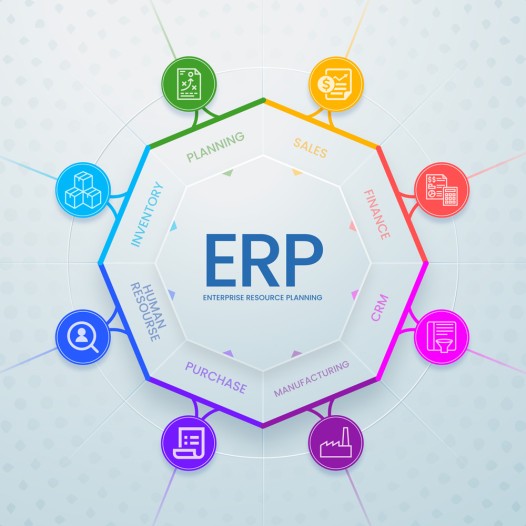
Why Datamation
Pioneer in ERP Solutions
Four Decades of Excellence Experience counts! With a proven track record of developing successful ERP solutions for over 400 clients across various business verticals, our expertise stands the test of time. Trust us to deliver innovative solutions that stand the test of time.
Customized Business Solutions
At our core, we understand that every business is unique. That's why we take a personalized approach to develop customized ERP solutions that cater to your specific needs, We empower you to achieve your goals with tailor-made solutions
Enterprise Grade Solution
At the heart of our ERP platform lies an unwavering commitment to quality. Our skilled team is continuously developing and improving the platform, ensuring that it meets the highest standards of excellence. This enables us to rapidly customize and deploy solutions tailored to your unique business needs.
Vision & Mission
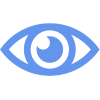
Vision
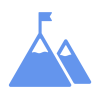
Mission
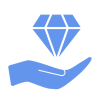
Values
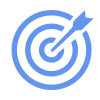
Goal
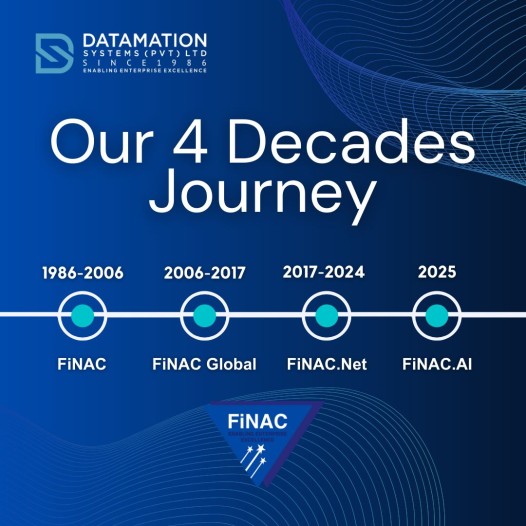
40 Years of Success
Celebrating 40 years of excellence and trust
Since 1986, Datamation Pvt Ltd has been in the FINAC industry, and we are a leading company in this field.
Value Proposition
- Achieving Success
Our track record boasts 100% successful implementations. - Client Satisfaction
Our extensive base of satisfied clients actively refers to us. - Sector Expertise
We bring business and process knowledge across 12 vertical markets. - Tailored Solutions
Customize FiNAC to perfectly fit your unique requirements. - Best Practices
Access world-class features and adopt industry-leading practices with FiNAC. - Efficient Implementation
Benefit from disciplined delivery cycles through data-driven processes and agile methodologies.